Case studies
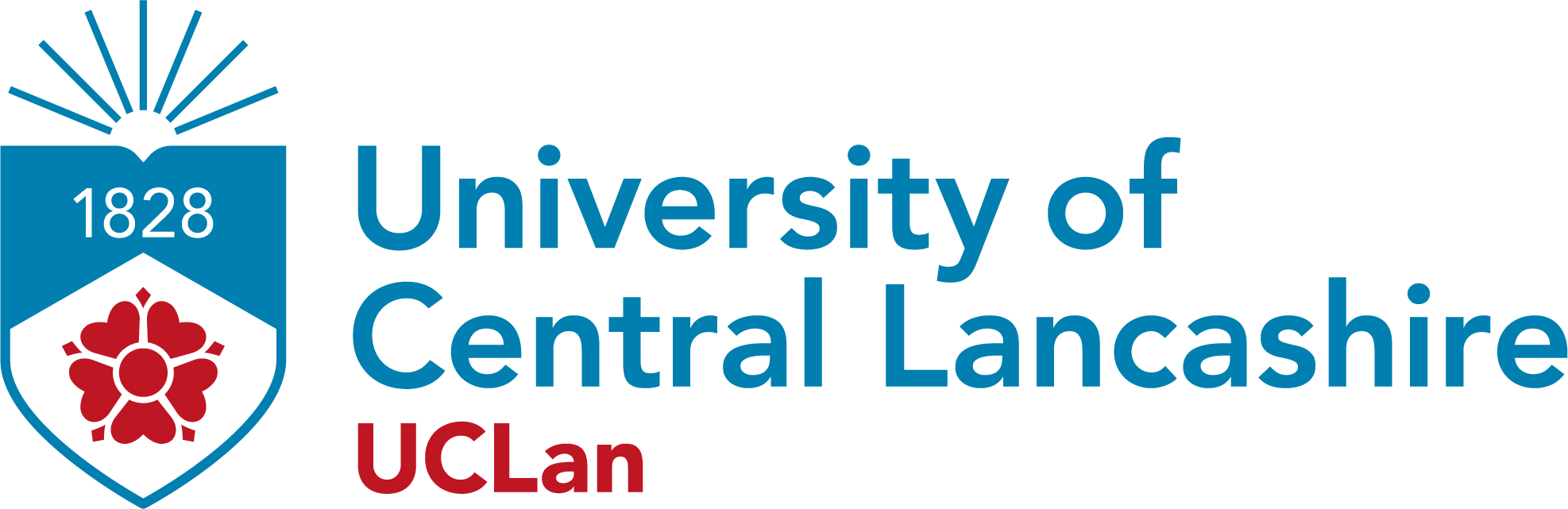
Degrees of development
The University of Central Lancashire is an international, multi-campus university that can trace its roots back to 1828. The institution leads the way in modern learning offering a range of Higher…
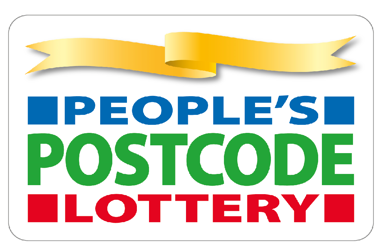
Cultivating cyber resilience: Case study - People’s Postcode Lottery.
In a recent conversation, Mark Sandison, the Technical Compliance Officer at People’s Postcode Lottery, shared how a physical penetration test conducted at their Edinburgh office proved invaluable…
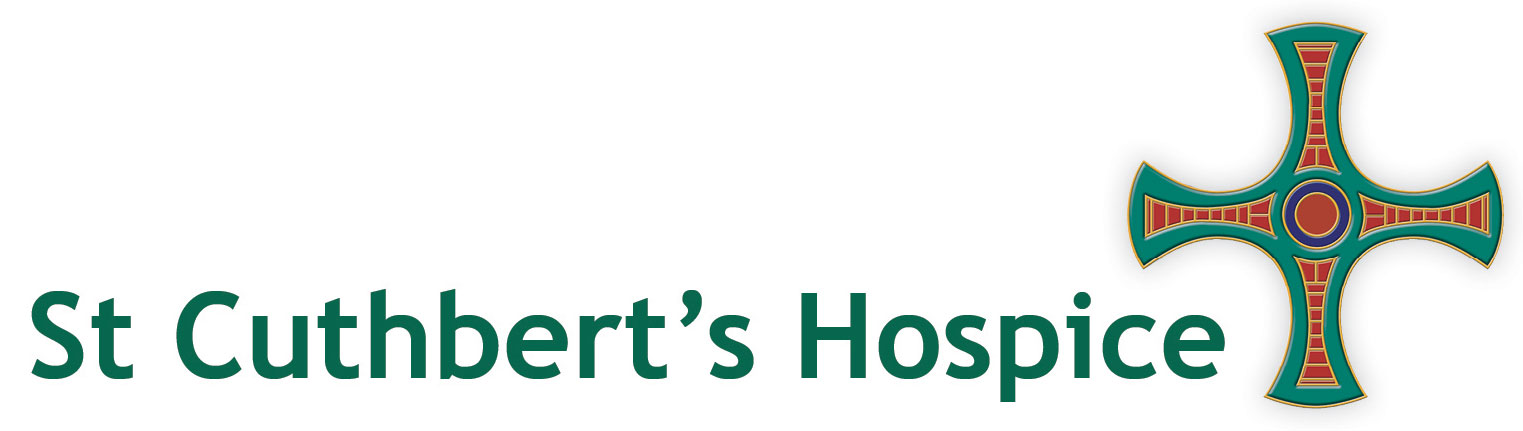
Smarter routes, bigger impact: How Waterstons transformed tree collections
The annual Christmas Tree Recycling programme at St Cuthbert’s Hospice is a vital fundraiser, but behind the scenes, the process was as complex as it was time-consuming.
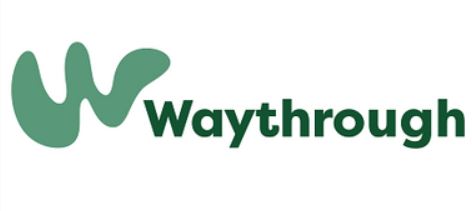
Finding a Waythrough the merger
Waythrough is a charity specialising in mental health, alcohol, drugs and related areas, formed from a merger of two like-minded organisations. They engaged Waterstons to plan and carry out the…
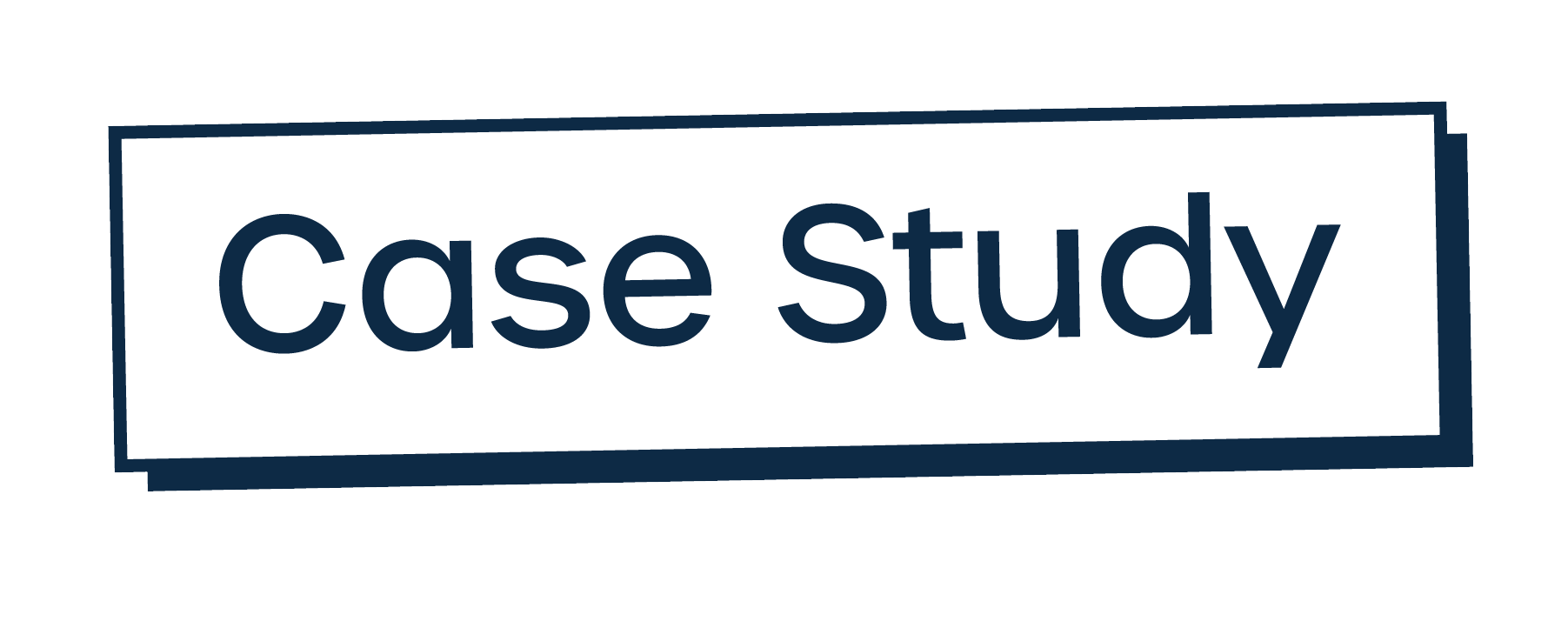
Agility through collaboration
Engaging with an administrative services provider to enable agile service deployment and ensure ISO compliance.
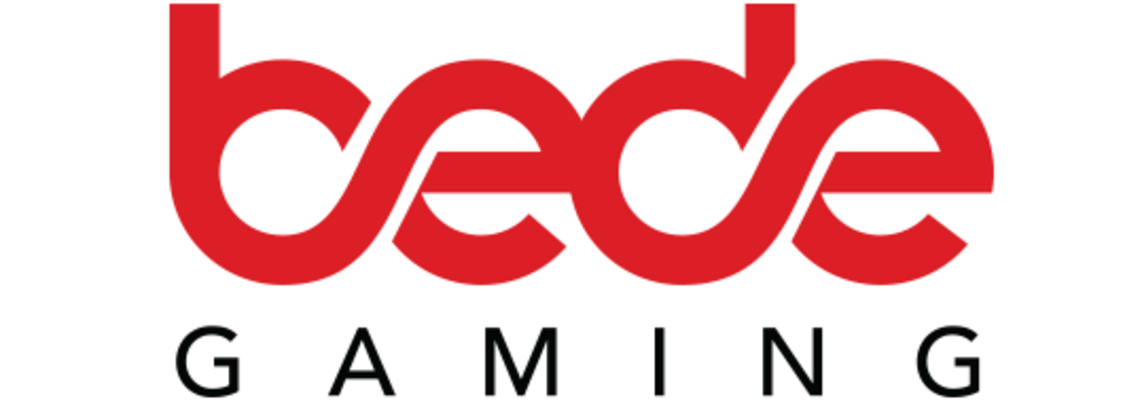
Jira Housekeeping for Bede Gaming
When completed, the Jira housekeeping project enabled Bede Gaming to improve delivery processes, reduce their operating costs, and better manage their Atlassian stack through Waterstons' technical…
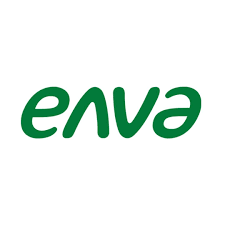
Implementing processes that deliver results
Enva is a leading provider of recycling and resource recovery solutions, managing hazardous and non-hazardous materials, hydrocarbons and general waste recycling. Recovering a broad range of waste…
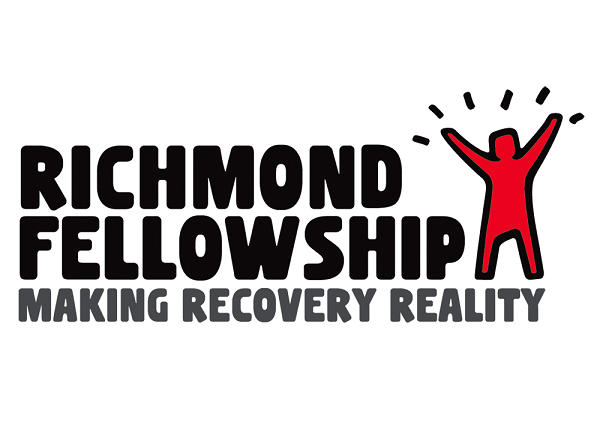
Creating order from chaos – Richmond Fellowship’s data revolution
Using Data as a Service meant that Richmond Fellowship didn’t need a big, expensive team to cover all its data needs, but could pick those that would be most useful at the time and supplement…